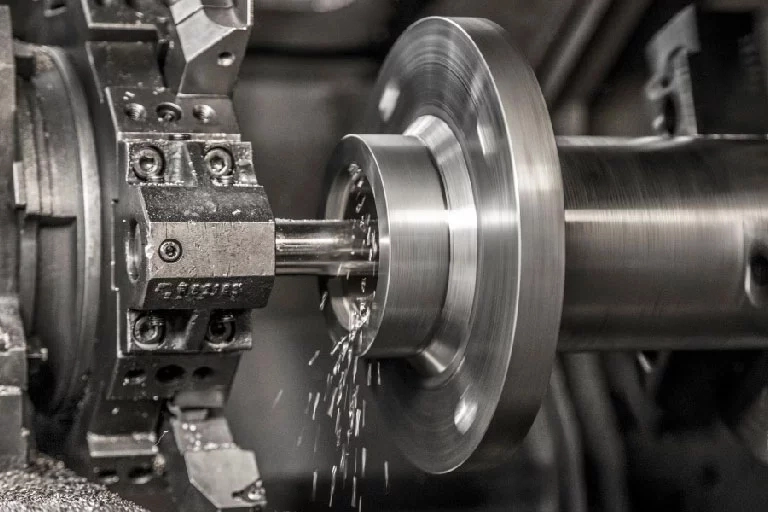
A lathe machine is a fundamental tool in the field of machining and manufacturing. It plays a pivotal role in shaping raw materials into finished products with precision and accuracy. Let’s delve into the mechanical workings of a lathe machine and its essential components:
Introduction to Lathe Machines:
A lathe machine is a versatile tool used for various machining operations such as turning, facing, taper turning, threading, and more. It rotates a workpiece on its axis while various cutting tools are applied to remove material, resulting in the desired shape and dimension.
Key Components:
- Bed: The bed is the base of the lathe machine. It provides support and rigidity to other components and ensures the accurate alignment of the entire machine.
- Headstock: The headstock houses the main spindle, which holds the workpiece and rotates it at various speeds. It also contains mechanisms for controlling spindle speed and power transmission.
- Tailstock: The tailstock is located on the opposite end of the headstock. It can be moved along the bed and is used to support the other end of the workpiece. It often includes a quill for drilling or other operations.
- Carriage: The carriage moves along the bed and carries the cutting tool and tool holder. It consists of the saddle, cross-slide, and compound rest. The movement of the carriage allows for longitudinal, transverse, and angular cuts.
- Apron: The apron is attached to the saddle and houses mechanisms for engaging the feed and threading processes. It also contains the gearbox for changing feed rates and thread pitches.
- Chuck: Chucks are used to hold the workpiece securely in the headstock spindle. There are various types of chucks, such as three-jaw chucks, four-jaw chucks, and collets, each suited for different applications.
- Tool Post: The tool post is mounted on the carriage and holds the cutting tool. Quick-change tool posts enable efficient tool changes, reducing downtime.
Mechanical Operations:
- Turning: Turning is the primary operation performed on a lathe. It involves removing material from the workpiece’s outer diameter to create cylindrical shapes or achieve specific dimensions.
- Facing: Facing is the process of cutting material from the end of a workpiece to create a flat surface perpendicular to the axis. It ensures a clean and precise surface finish.
- Taper Turning: Taper turning involves creating a gradual decrease or increase in diameter along the length of the workpiece. This is achieved by adjusting the angle of the cross-slide.
- Threading: Threading is the process of creating external or internal threads on a workpiece. This is crucial for creating screw threads, bolts, and nuts.
- Knurling: Knurling is a process used to create a textured pattern on the surface of a workpiece, providing better grip and aesthetics.
- Boring: Boring enlarges or refines existing holes in a workpiece using specialized boring bars and cutting tools.